As an insulating material manufacturer, you know the importance of your products performing reliably and safely under harsh electrical conditions. One major threat is electrical arcing - when a high-voltage discharge burns across or through an insulator. This can lead to failure, fire risks, and safety hazards.
That's why arc resistance testing according to ASTM D495 is so critical. This standardized test, developed by the leading standards authority ASTM International, allows you to evaluate just how resistant your insulating materials are to arc tracking and breakdown.
Key benefits of arc resistance testing
By undergoing ASTM D495 testing, you gain valuable insights that translate into superior product performance and safety:
- Safety Validation - Know with confidence that your insulation can withstand repeated high-voltage arcing without allowing a conductive path to form through tracking or carbonization. This prevents arc propagation and safeguards your product.
- Early Detection - The test is designed to screen new formulations and detect even subtle changes that could impact arc resistance. This helps you catch issues early before products go to market.
- Quality Control - With consistent arc resistance testing, you can monitor production quality over time and ensure every batch meets your high standards for arc performance.
- Time-Proven Approach - While no lab test is perfect, ASTM D495 has been refined over decades to provide a realistic yet controlled method for evaluating arc resistance under accelerated conditions.
How arc resistance testing is performed
In the ASTM D495 test, your material samples are subjected to an intermittent high-voltage, low-current arc discharged along the surface. The time until failure modes like tracking, carbonizing, or ignition is precisely measured. The test progresses through increasingly severe stages by reducing pause time between arcs or boosting the current level. This allows for meaningful comparisons between different materials and formulations.
While ideal for screening and quality control, ASTM also recommends supplementing D495 results with other tests that simulate wet, contaminated conditions for a complete engineering analysis.
Why choose Element?
Don't leave your product's arc resistance performance to chance. Leverage the power of ASTM D495 testing to ensure safety, quality, and a competitive advantage. Our team of experts is equipped to perform these critical evaluations accurately and efficiently.
Request a quote today for comprehensive arc resistance testing per ASTM standards. Stay ahead of the curve and give your customers premium insulating materials they can count on.
Learn more
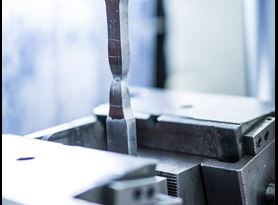
Materials Testing
Find out more about Element's comprehensive ranges of materials testing services available in the TIC sector, covering materials selection, application and performance testing as well as failure analysis testing services.
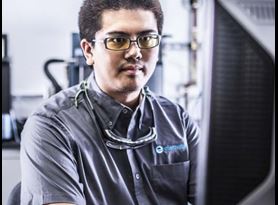
Composite Testing
Find out about Element's composite testing support in material selection and qualification, materials testing, fatigue testing, manufacturing process development, failure analysis, repair technology and training.
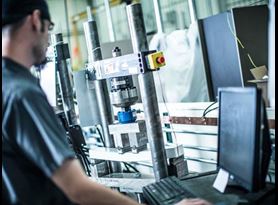
Mechanical Testing of Polymers
Find out about Elements unique range of mechanical testing services for polymers, elastomers, thermoplastics, composites and structural adhesives.
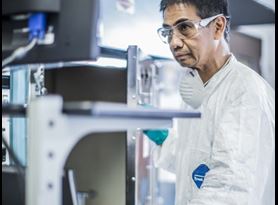
Thermal Analysis (DSC, TMA, DMA, TGA)
Thermal analysis methods measure mechanical changes under differing temperatures and loads, and can pinpoint when and at what temperature significant thermal events occur.