Element’s industry-leading laboratories host the latest digital radiography testing equipment that can quickly and efficiently identify weaknesses in your materials. Our experts use this powerful non-destructive testing method in the aerospace, energy, and manufacturing sectors to make certain your products are compliant and fit for purpose.
Digital radiography (DR) is used for non-destructive testing and examination of the internal features of a product, to characterize materials properties, and to identify defects. It is an advanced form of conventional ‘film’ radiographic testing, an x-ray image is displayed directly onto a computer screen, producing real-time results.
Digital radiography testing methods
Element’s digital radiographic test methods capture inclusions digitally using Digital Detector Arrays (DDA) and reusable imaging plates, instead of traditional methods using x-ray film. We use three main test methods for digital radiographic testing:
- Computed radiography (CR) is the simplest digital radiography method. The item is exposed by x-ray tubes in cabinets, the imaging plate (IP) captures the image, and the IP is digitally scanned for display onto a high resolution viewing monitor.
- Digital radiography uses a digital detector array, also known as a flat panel detector, with specialized x-ray tubes. The detector is rigid, exposure times are 70-90% shorter, and labor costs are significantly reduced. The image capture speed for DR is faster than alternate methods.
- Computed tomography is an extension of DDA technology. It uses an automated detector motion to gather thousands of digital images at various angles to create a 3D image.
In our article The Difference Between Computed Radiography (CR) and Digital Radiography (DR) blog, we explain the three common NDT digital radiography modalities, their uses, and their benefits.
Our global experts are Level 3 qualified and on hand, ready to recommend the most suitable testing methods for your upcoming projects.
Advantages of using digital radiography testing
Digital radiography provides excellent image quality and a high probability of detection (POD). It is more economical than conventional radiography techniques; no film or developing costs are required, and plates can be re-used. The radiographic images are stored digitally and can be sent electronically by senior technicians to customers to view, saving valuable image processing time. Due to the elimination of film, digital radiography is also more environmentally friendly and can lead to more attractive pricing.
- High-quality images
- High probability of detection
- Lower cost compared with conventional radiography
- No film and film developing costs
- Reusable plates
- Reduced image processing time
- Low environmental impact
The Element advantage
Element is the leading testing and inspection company for the aerospace, energy and product testing sectors. Our testing experts ensure the quality of your finished products and materials while delivering the certainty your radiographic inspection projects require.
We offer a range of digital and computed radiography solutions that are suitable for many industrial applications.
Please contact our experts now for more information.
Related Services
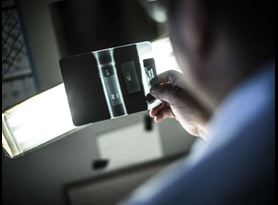
Radiographic Inspection Services
Our RT laboratories are staffed by certified technicians and knowledgeable engineers utilizing state-of-the-art equipment and instrumentation.
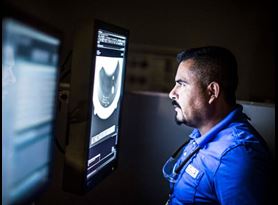
Non-Destructive Testing (NDT)
Find out about the range of NDT services Element uses to evaluate the properties of a material, parts, products, welds, or systems without materially affecting the integrity of the items being tested.
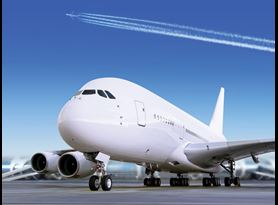
Aerospace Testing
Find out about our materials and product qualification services and our specialist support for the global Aerospace Testing sector.
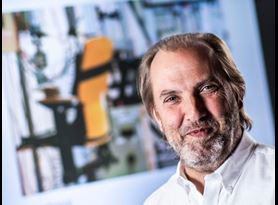
Digital Radiography Webinar
What are the different methods of Digital Radiography testing? What are the strengths and limitations of each? Which technique should I use? Watch our on-demand webinar to learn more.