Testing and qualifying advanced elastomers for deepwater oil exploration

By Engaged Expert
Glyn MorganGlyn Morgan is an expert in the application of elastomers, thermoplastics and composite polymer materials within the Oil and Gas sector.
The numerous and varied challenges to deepwater oil extraction have meant that, for many decades, the Oil & Gas industry has been identifying and extracting ‘easy’ reserves of natural Oil & Gas.
However, such deposits are becoming increasingly rarer. In recent years, the trend towards colder, deeper and more hostile environments has been demonstrated by the discovery of mega-fields, such as that off the coast of Brazil. The industry can now be said to be intensely focusing on deepwater exploration. A 2013 report by Douglas-Westwood states that over US$232 billion will be spent on deepwater projects between then and 2020. Such levels of investment indicate the challenges which are anticipated by E&P companies in accessing oil at depths of up to 3 km below sea level.
While the projected figures highlight that the most apparent challenge is one of cost (deepwater projects are, of course, more costly than onshore or fixed offshore operations), the Majors anticipate that they have few alternatives. Rapidly-emerging economies, such as India and China, are fueling global energy demands, which show no sign of diminishing, and oil is set to remain as the most dominant power source for the near future. It is this demand which ensures that such complex, expensive endeavors are economically viable and it is the technical challenges of deepwater extraction, rather than the financial ones, which producers must face.
Fields at a depth of 2 km and more display a unique set of peculiarities which make the deployment of standard equipment unfeasible. One particular technical issue is the occurrence of unusually high levels of CO2 in the production stream. This emerges from the reservoir in a super-critical state – at a temperature exceeding 31°C and at a pressure of 74 bar. In this state, the CO2 exists as a dense phase fluid and displays the characteristics of both a liquid and a gas. This poses severe technical challenges when it is deployed from the well to the surface. Components such as valves and blowout preventers are under attack from not only the super-critical CO2, but also by damagingly high levels of corrosive HS2 which are present in deepwater environments. The CO2 can be used advantageously if it is injected back into the reservoir to reduce the viscosity of oil and assist its flow back into the well.
Following the success of the Statoil Hydro-operated Tordis field in the North Sea, such full-field subsea separation, boosting and injection systems are now widespread. In 2007, Tordis increased its recovery by an extra 35 MMbo and extended the life of the field by an extra two years to 17 years. Due to the higher pressures and temperatures encountered in deeper water, persistent corrosion, pressure and temperature issues all begin to create problems for technology. The compressors used, for example, must be able to withstand any damage caused by harmful gases in order to avoid critical failure.
Elastomer selection and qualification
Currently, Element is involved in the research, development and qualification of next-generation materials which are designed to offset the problems encountered during deepwater extraction. One such material is elastomers which, thanks to their pliant, flexible nature, are ideal for use in sealing components. A recent project saw a client looking to operate a recently-discovered 2 km deep field off the Brazilian coast. Element was approached to characterize a range of advanced, proprietary, commercially-available elastomers.
At this depth, the extreme operating conditions can make elastomers more vulnerable to chemicals which can structurally alter them. The valves and components into which they are formed come into contact with Oil & Gas at 120°C and must contend with rapid gas decompression and high pressure events. The qualification and selection of the best materials for this environment, therefore, is critical.
Of the many elastomers available, seven well-characterized primary products were chosen for qualification. They were selected to deliver optimum performance and in order to represent the three core varieties of elastomer:
- Hydrogenated Nitrile Butadiene Rubber (HNBR)
- Fluoro-elastomer (FKM) and
- Perfluoro-elastomer (FFKM).
Each type of elastomer has its own particular strength. FFKM is ideally suited to a high temperature and chemically-aggressive environment, while HNBR is considered to have a wide range of positive properties and performs well at lower temperatures. FKM finds the middle way between the other two, offering good resistance to thermal and chemical environments as well as gas decompression events.
The primary concern for engineers when selecting an elastomer for these components is rapid gas decompression and pressure resistance. However advanced the material is, over time and under pressure damaging chemical elements, such as super-critical CO2 and HS2, will permeate the polymer. If rapid decompression occurs, the pressure changes mean that gases are forced out of the material, potentially blistering or cracking it as they escape. Under constant pressure, the fluid that has diffused into it can cause the material to swell and weaken, potentially causing leakage and loss of integrity.
In order to overcome this, elastomer producers have been developing new grades which are engineered at a molecular level to be more reliable and robust than previous varieties. The products chosen for qualification by Element were relatively new, with the most recent developed only 18 months ago, and one in particular, a FFKM specifically engineered to withstand gas decompression – a major historical weakness of this elastomer type. Material scientists have also extended the limits of HBNR, with one tested example showing unprecedented high pressure resistance.
Pressure testing elastomers
The team subjected the seven products to a variety of tests in order to qualify them and provide comprehensive statistical data which would allow for accurate assessment. Tests were undertaken at specific temperature ranges, pressures and fluid ratios to simulate the existing environmental conditions at the well and over the required lifetime of the component. The tests focused on three primary areas of interest – long-term ageing, mechanical performance, and rapid gas decompression performance.
The program was conducted over a year in order to perform an extensive test matrix. Six months of this was dedicated to performance testing all seven products to ensure that all were capable of withstanding long-term exposure to a variety of fluid chemical elements. This required seven high-pressure exposure tests of up to 626 bar and 100 °C, with multiple combinations of water, oil, CO2, HS2 and methane. In order to perform these high-pressure exposures, bespoke stainless steel pressure vessels were designed and used in house. Each has a wall thickness of 5 cm and an approximate capacity of 3 liters, which enabled the testing of each elastomer at the required pressure of almost 1,000 pounds psi. These exposure tests monitored swelling, changes in hardness, change in compression set, and tensile properties after one, three and six-month periods.
To qualify the effects of decompression and material performance, the products were also subjected to three individual rapid decompression test scenarios, again at 626 bar and 100°C, in order to simulate the operational deepwater environment. In addition, Element designed an innovative pressure system with a custom-built sapphire-based viewing window. Standard pressure vessels are sealed at each end with sapphire windows, which allow observers to view and record proceedings inside the pressurized environment. A variety of fluids can be pumped into the vessel where the sample is mounted, which allows for the physical observation of the material, such as a seal, under a wide range of simulated conditions until it either ceases to function or develops physical damage.
This unique methodology not only allowed for the recording of different swell rates under gas decompression of the different elastomer products while they were exposed to super-critical CO2, but also allowed for the charting of the exact point at which material changes occurred – additional data which was previously unobtainable to the producer.
Results and conclusions
The outcome of the program provided a definitive list which ranked the seven elastomer products, and identified those which were best suited to the specific deepwater environment simulated. Two emerged from the testing with significantly superior performance results across the range of tests, and it was these which were recommended for operational use. One particular HBNR displayed impressive resistance to damage under rapid decompression – when taken as a benchmark, a comparable product, which was tested several years before, suffered noticeable cracks in a cross section of the tested sample. Under identical conditions, and viewed in situ through the sapphire-based window, the best performing HBNR is characterized by uniform resistance.
This HNBR’s operational integrity was also unaffected by super-critical CO2 – after benchmarking performance levels under conditions with heavy levels of both super-critical CO2 and HS2, tests could be repeated without the presence of hydrogen sulphide to show if the CO2 produced any negative reactions. While HS2, in conjunction with super-critical CO2, has a highly damaging effect over six months, as expected, super-critical CO2 alone produced negligible performance fluctuations.
If it were not for advanced materials such as these elastomers, component designers would have to rely on metal-to-metal seals. These do not possess the performance threshold of new elastomers and would raise significant engineering challenges. Elastomers’ superior performance demonstrates the material’s versatility – it is inherently flexible which makes it ideally suited for various offshore technologies such as bonded hoses carrying oil from ship to ship. It is also capable of operating at a range of temperatures and pressures and its more robust examples can be formed into larger diameter products which are less likely to fracture when deployed in heavy, rolling seas.
At these largely unexplored depths, even something as tiny as a single valve plays a crucial part and needs to be fully functioning to maintain its integrity for up to 30 years. Advanced materials are enabling the Majors to operate their multi-billion endeavors at deepwater levels, thanks to the performance of their smallest components. It is only through the process of rigorous testing and qualification that confidence is generated in advanced materials which are selected to support production and make the technical challenge of E&P in deeper, colder and more extreme environments a little less challenging.
Find related Resources
More from Element
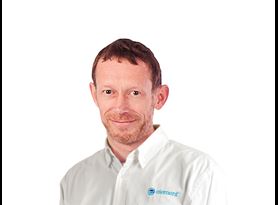
Glyn Morgan
Glyn Morgan has over 20 years experience in the application of Elastomers, Thermoplastics and Composite Polymer materials in the Oil and Gas sector.
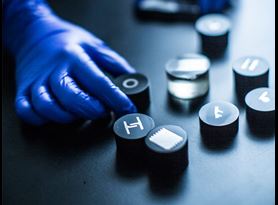
Materials Characterization
Find out how Element helps its customers to characterize, evaluate, select and apply metals, polymers, rubbers and elastomers in their end products and applications.
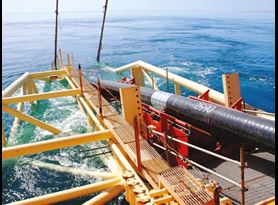
Coatings Testing
We offer world-class materials expertise in polymers, elastomers, thermoplastics, composites, and structural adhesives. With a global reach of coatings laboratories in the UK, USA, Europe, and Asia, Element provides a comprehensive range of coatings testing services to the Energy, Aerospace, Defense, and Transportation sectors.
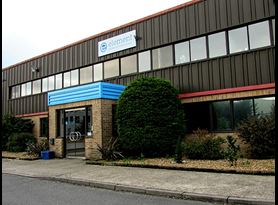
Element Hitchin
As Element's Global Center of Technical Excellence for Polymers, Element Hitchin has decades of experience providing a comprehensive range of highly specialized services.