5 Considerations for ASTM D3039 Composite Tensile Testing

By Engaged Expert
John MoylanJohn Moylan is a senior expert in the testing of polymer based composite materials for the global Aerospace sector.
The ASTM D3039 testing methodology is a great choice for polymer matrix composite tensile testing because of its usability across a wide range of industries.
In fact, ASTM D3039 is called out by CMH17, formerly MIL-HBK-17, for the determination of design allowable values for tensile strength, modulus, and Poisson’s ratio.
Additionally, ASTM D3039 is used as a quality control tool for composite fiber overwrap applications. In these applications, composite overwraps are applied and cured on-site to concrete columns for seismic reinforcement. Composite tensile testing provides evidence that the material has been laid up and cured per manufacturers’ instructions.
ASTM D3039 - a Standard Born out of Necessity
Decades ago, producers of composite materials faced a problem. When it came time to test their products for strength and safety, the only available test methods were standards developed by and for the plastics industry. Various aerospace firms developed their own proprietary standards to meet their needs.
To obtain tensile properties representative of the materials, and to work toward industry standardization, the ASTM D30 committee developed ASTM D3039, a consensus standard for polymer matrix composite tensile testing. Since the 1970s, this specification has grown to become the most popular composite tensile testing standard in use today.
5 Considerations for Composite Tensile Testing per ASTM D3039
Before embarking on a testing program using the ASTM D3039 testing standard, there are a few considerations to make, including the type of material, panel thickness, specimen machining and tabbing, and proper test controls.
1. Know your Material
The ASTM D3039 testing methodology is specific to continuous high-modulus, reinforced polymer matrix composites (that is to say, polymeric materials that contain reinforcing fibers, like carbon or aramid). Matrix materials include epoxies, bismaleimides (BMIs), polyamides, and thermoplastics such as PEEK.
If your material is discontinuously reinforced, ASTM D638 generally is a better-suited test method. Likewise, ceramic matrix composite materials are generally tested to ASTM C1359, and metals to ASTM E8.
2. Specimen Thickness
ASTM D3039 testing specimens are usually machined from flat-cured panels. Ideally, the panels should be between 0.040 inches and 0.200 inches depending on the layup. Any thicker, and specimen may fail in shear at the gripping area or internally prior to reaching the true tensile strength of the material. Any thinner, and specimen will be unnecessarily affected by environmental factors, like the surface stress along the grips.
3. Machining of Specimens
Proper machining of ASTM D3039 testing specimens is crucial to obtaining results representative of the material, with low scatter. The specimens are rectangular with a uniform thickness cross-section. The best practice is to grind the edges of each specimen to insure parallelism and a good surface finish. The standard requires less than 64 rms, but Element generally obtains less than 20 rms.
While machining, it is important to be within 0.5 degrees of the fiber direction. Grinding specimens to thickness is not appropriate due to fiber path damage.
4. Tabbing of Test Specimens
To achieve an accurate determination of composite tensile strength, the gage area must have a nearly uniform stress distribution. The use of end tabs helps introduce the load from the grips to the specimen in a uniform way. Tabs are not always required or even desired. With carefully aligned hydraulic grips and an appropriate gripping surface, woven composites, 90-degree tape, and +/- 45-degree layups may be tested more effectively without tabbing. Zero-degree tape lamina specimens are best tested with tapered tabs.
Regardless of the tab type utilized, the test machine grips should extend past the end of the specimen tabs.
5. Test Alignment and Control
Test machine grip alignment is also critical to obtaining accurate results with ASTM D3039 testing. Generally, hydraulically loaded grips are used. The alignment of the grips is adjusted and verified with a bar with 9 strain gages, assuring the loading is pure tension, without bending.
Strain may be measured with a calibrated extensometer or strain gages. Modulus is most often calculated between 1000 and 6000 microstrains. Biaxial strain measurements are used to obtain Poisson’s ratio.
The entire load train may be heated or cooled in an environmental chamber so the tensile properties can be characterized from cryogenic temperatures up to the degradation temperature of the material.
The Element Advantage for ASTM D3039 testing
Choosing the right testing methods for your materials is often just as important as the results you receive. Having a working knowledge of the material type, end application, and testing requirements will help ensure that you choose the right test methods. If you are in need of polymer matrix composite testing and are considering the ASTM D3039 testing methodology, an accredited lab can help you make informed decisions, allowing you to get the most valuable insights possible. The more you know about your materials, the better they will work for you – for years to come.
For more information contact our experts today.
Find related Resources
More from Element
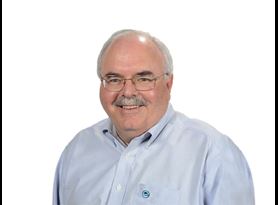
John Moylan
John is a long standing and highly active member of multiple committees within his field and is highly regarded as an expert in all polymer based composite materials.
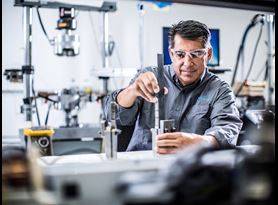
Polymer Matrix Composite Testing in Aerospace
Polymer Matrix Composites (PMCs) are helping push the limits of aerospace technology with lighter, stronger, more durable materials.
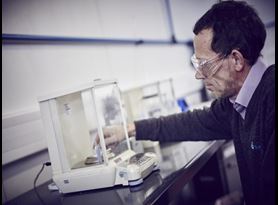
Polymers Testing
Element performs a range of mechanical, electrical, flammability tests and utilizes thermal analysis tests to characterize the composition of polymers and composite materials.
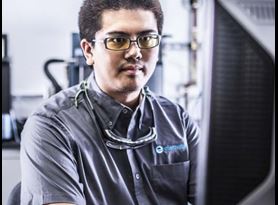
Tensile Testing of Composites
ASTM D3039 determines the ultimate tensile strength, ultimate tensile strain, tensile chord modulus of elasticity, Poisson’s ratio and transition strain of Polymer Matrix Composites (PMCs).