Pulsatile Durability Testing of Complex Intravascular Devices
Pulsatile durability testing is performed to evaluate an intravascular device’s resistance to fatigue failure.
Intravascular devices are typically placed within straight mock arteries for testing, mounted onto a stent/graft tester and subjected to cyclical pressure pulses. The pulses create a dynamic radial strain in the mock artery that simulates in vivo strain levels that occur due to the expansion and contraction of the surrounding vessel.
Complex intravascular devices
While many device designs are tested using straight vessels, complex device geometries occasionally require the development of custom mock arteries to simulate target deployment sites. If custom mock vessels are introduced, additional validation and feasibility testing are required.
Examples of such devices include left atrial appendage occluders to prevent strokes in non-valvular atrial fibrillation patients, neurovascular embolization coils for complex brain aneurysms, endovascular aneurysm repair devices of abdominal aortic aneurysms, and devices for arteriovenous fistulas.
Custom mock artery test apparatus
MDT (now Element) designed the ElectroForce 9100 Series of Stent/Graft testers specifically for pulsatile durability testing. Its dual motor design is perfectly suited for custom applications as it allows tweaking of the amp of one of the motors to get more uniform strains and improved strain distribution across the length of larger vessels, including Abdominal Aortic Aneurysm (AAA) devices. Single motor stent testers lack this capability.
The ElectroForce 9100 instrument features 4 to 12 mock arteries mounted between a pair of manifolds and linear-motor-driven pumps. The computer-controlled system delivers radial strain to intravascular devices under controlled temperature conditions, and a laser micrometer measures radial strain at various positions along the length of each device to ensure that desired strain levels are met throughout testing.
The manifolds are modular and allow mounting customization of mock vessels and diameters to match each application such as the neurovascular coil testing shown below (left image).
The setup below (right image) was used for pulsatile fatigue testing of 8 left atrial appendage occluders (two per station) at 40 Hz and 37±2°C in isotonic saline solution. Testing was performed per ASTM F2477-07 (2013) and ISO 25539-1:2003/Amd1:2005 (now incorporated into ISO 25539-1:2017). The mock silicone vessel has two segments, a smaller diameter section and a step-up larger diameter section to accommodate the occluder geometry.
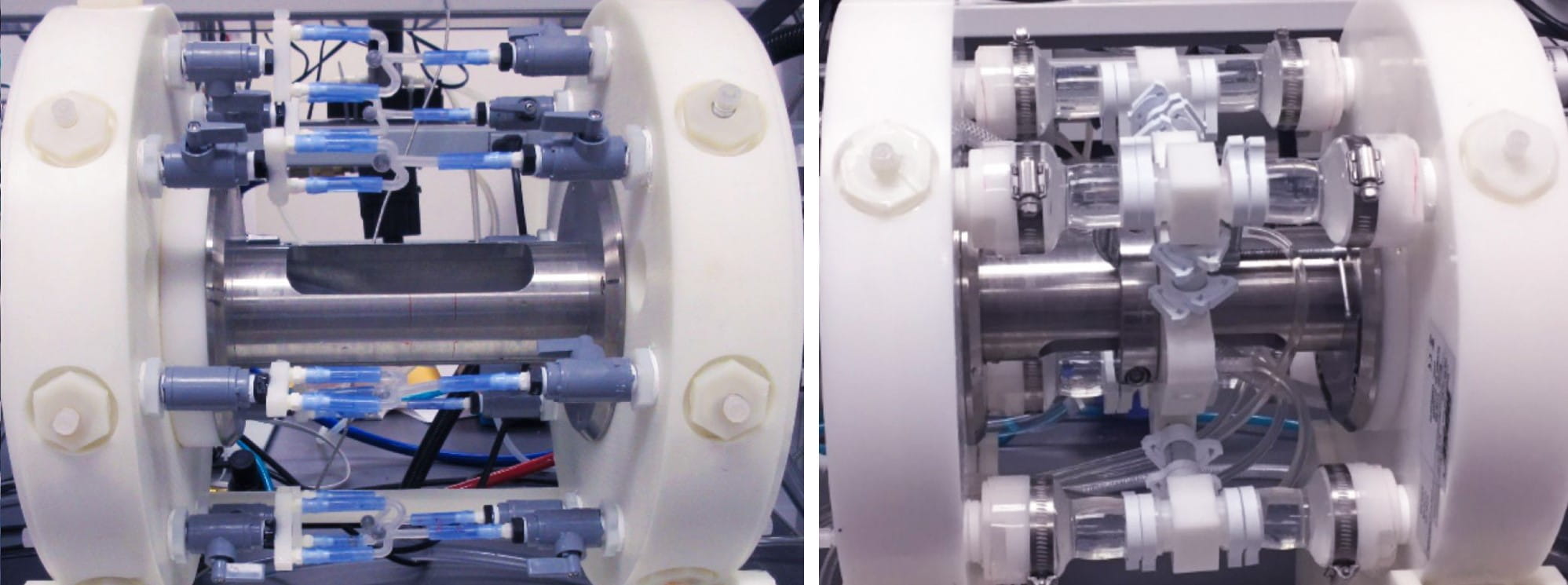
Steps for pulsatile durability testing of intravascular devices
The table below outlines the main steps of a standard experimental protocol. If custom mock vessels are introduced, additional validation and occasionally feasibility testing take place to ensure that devices are reaching target strain levels.
- Inspect test vessels and document observations
- Perform vessel conditioning on the pulsatile test system
- Deploy devices into the test vessels
- Inspect devices and document observations
- Install deployed vessels onto the pulsatile test system
- Fill pulsatile test system with saline or distilled water and control the temperature to 37°C
- Begin cycling and adjust the mean pressure to achieve the vessel diameter target
- Adjust volumetric displacement or ΔP to achieve the strain target
- Start fatigue test once targets are achieved
- Monitor the test daily for target compliance and stability
- Inspect devices at interim timepoints in accordance with the test protocol
Designing the right mock arteries
Design requirements for the custom mock vessels are typically obtained from published data in the literature and/or finite element analysis. The two main outputs are vessel geometry and compliance. To simulate physiological vessel compliance, these mock models are often manufactured from silicone as shown below.
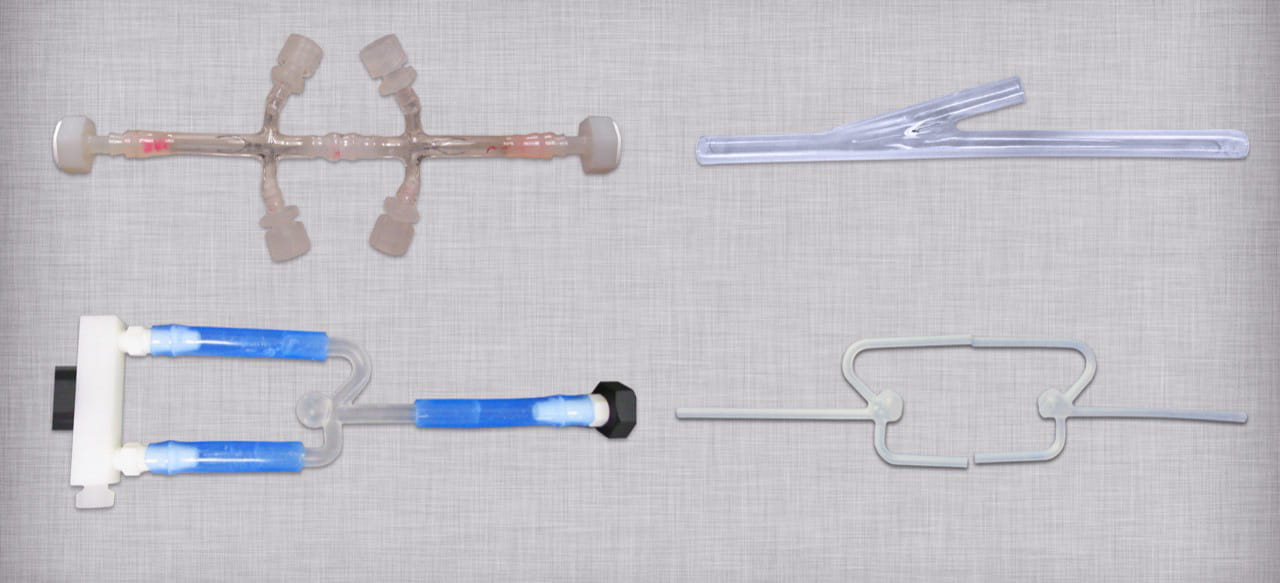
Validation testing focuses on strain and compliance targets. In some applications, reaching the target strain level is more important than vessel compliance. However, compliance targets are critical in physiological modeling applications.
A laser micrometer is used to measure strain validation by mapping strains along the custom mock artery and making instrument adjustments until reaching the target values. Similarly, target vessel compliance is verified by taking outer diameter measurements with the laser micrometer and converting these values to inner diameter. Calibrated pressure transducers measure pressure levels, and compliance is calculated per the equation below:
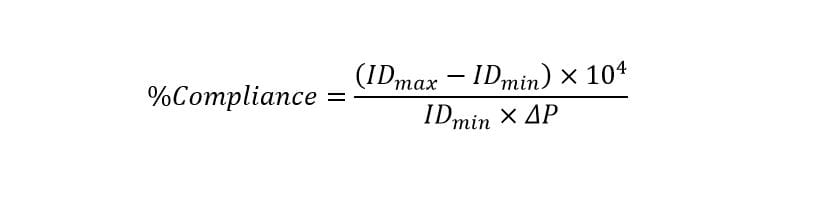
In summary, complex device geometries and deployment sites often require the development of custom mock arteries. This complexity added to the test setup requires additional validation to ensure that devices are subject to the desired test conditions.
How can we assist you?
Our Engaged Experts excel at intravascular pulsatile durability testing and have worked with many challenging device designs and test setups over the last several decades. Contact us to discuss how we can help with your test project.
Element Materials Technology is ISO 17025 accredited and has one of the most expansive medical device testing scopes in the world ranging from orthopedics and cardiovascular implants testing to EMC/EMI/product safety testing, and biological and packaging evaluations.
Find related Resources
Related Services
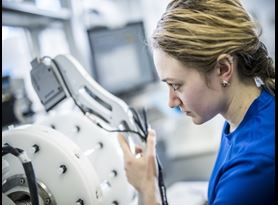
High Speed Stent and Graft Testers
Our medical device manufacturing customers are regularly challenged with short timelines to bring products to market.
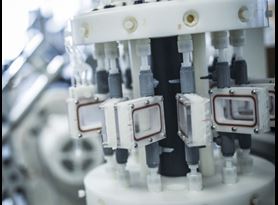
Cardiovascular Device Testing
Element specializes in a wide range of testing for cardiovascular devices, such as stents, grafts, occluders, catheters, heart valves and pacemaker leads.
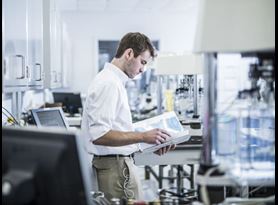
Test Protocol for Medical Devices
A protocol and plan will mitigate your risk, prevent confusion, set clear expectations, and preserve the necessary information for future reference and use.
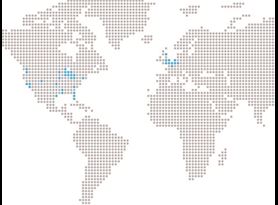
Element Locations
Learn more about our laboratories - where they are located; the unique capabilities they have and how they can help you solve your technical and commercial challenges.