With the ability to report accurate and detailed data about strain and compression profiles, digital image correlation (DIC) is a powerful tool for providing information about mechanical strength, material behavior, and stress characteristics.
Our experts use digital image correlation in conjunction with mechanical testing to record how a material or system moves during testing. Unlike traditional strain gauging, DIC can view and measure movement across an entire sample or component. It yields a more robust data set, allowing us to make better predictions about material behavior in real-world situations.
The Digital Image Correlation Principle
Digital image correlation uses a high resolution, high-speed camera to record how a sample changes over the course of a static or dynamic test. Prior to testing, the sample is painted with reference points that allow us to track the amount and frequency of movement. With the recorded data, we can create a strain profile for the entire piece of material or equipment, with accurate predictions about the behavior and life expectancy of the system as a whole.
While this method is available for a variety of applications, it is particularly useful for testing complex parts or unusually shaped samples. The inherent flexibility and versatility of DIC allows data to be taken from any point on a sample, no matter the size or shape. Testing can be performed on critical equipment and materials that would otherwise be extremely difficult to accurately test and characterize.
“The inherent flexibility and versatility of DIC allows data to be taken from any point on a sample, no matter the size or shape.”
Our Digital Image Correlation Software
Our labs have invested in state-of-the-art digital image correlation technology, allowing us to provide highly accurate data using the most advanced techniques currently available. Using a high resolution camera and high-powered in-house data processing, we are able to handle larger, more complex projects than ever before.
We can use digital image correlation to create a 3D, full-field map of a material or product, noting complicated surface features as well as strain characteristics and failures. To accommodate a range of test and material types, we use an adjustable base camera that gives us the freedom to integrate DIC into a variety of services, from high and low cycle fatigue to creep testing.
Our digital image correlation software and equipment has several distinct features, including:
- 3D mapping of deformation and strain up to 0.005% accuracy
- Identification of individual stress points
- Testing at ambient and elevated temperatures (specimen temperatures up to 1500 F)
- Frame rate up to 1,330 Hz
- 4M camera resolution
- In-house data processing software for managing extremely large files
"We can use digital image correlation to create a 3D, full-field map of a material or product, noting complicated surface features as well as strain characteristics and failures."
With enhanced resolution and flexibility, our digital image correlation capabilities are among the most advanced in the industry. For more information about our services, or to speak with an expert about DIC, contact us today.
Find related Resources
Related Resources
Learn more
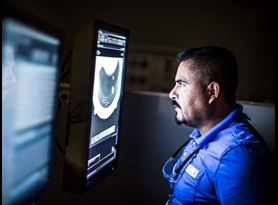
Non-Destructive Testing (NDT)
Element's NDT services comply with a wide variety of industry standards, government contracts, military specifications and unique customer requirements.
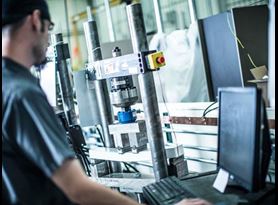
Mechanical Testing of Polymers
Find out about Elements unique range of mechanical testing services for polymers, elastomers, thermoplastics, composites and structural adhesives.

Mechanical & Destructive Testing
Element's mechanical tests are part of our destructive testing services, they show whether a material or part is suitable for its intended mechanical applications.
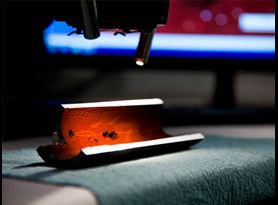
Failure Analysis
Find out how Element's global team of failure analysis experts learn from the past, to help prevent failures in service.