Knee Implant Contact Area & Contact Stress Testing

By Engaged Expert
Maciej JakuckiMaciej Jakucki has performed and managed a wide variety of medical testing projects and programs to meet FDA and CE requirements.
As the push for implants to be more wear-resistant and patient-specific continues, understanding a device’s contact stresses and contact areas is useful for evaluating one of the most common failure modes - insert wear. This article focuses on testing contact pressure and contact area for total knee replacements.
Over one million total knee replacements (TKR) take place on an annual basis in the United States. Knee implants are installed to reduce pain and ultimately bring the joints back into alignment. In previous articles, we’ve discussed testing the femoral and tibial components of total knee replacement, but this article will take a closer look at the ultra-high molecular weight polyethylene (UHMWPE) bearing used to replace a worn meniscus. This type of component helps to improve range of motion, create proper spacing and distribute loading to eliminate pain for the patient.
Meniscus degradation usually begins to occur as the load concentration, or stress, from the medial condyle increases due to wear, age, or disease. As a result, the condyles start wearing through the meniscus, which can ultimately result in bone on bone contact. Not only does this cause pain, but it also causes misalignment of other joints, which can lead to additional health problems. Total knee replacements are designed to re-align and appropriately distribute loading through both the materials and the contours of the bearing.
Total knee replacement tibial insert
The bearing (or tibial insert) is made of ultra-high molecular weight polyethylene (UHMWPE) which has high wear resistance properties, especially if it undergoes crosslinking or vitamin e enrichment processes. The implant material must hold up in static loading from activities such as standing, as well as withstand wear due to articulation against the femoral component during daily activities. A critical step in evaluating a bearing is quantifying the contact area and/or contact stress created between the femoral component and the tibial bearing. It is important to understand the effects stress or pressure can have on an implant, as the forces experienced during walking can be several times body weight. Therefore, stress distribution and contact must be taken into consideration when designing the matching contours.
When applying equal forces during testing, a small contact area will result in high stresses while a larger contact area will result in less significant stresses. Increased stress over time can contribute to delamination or creep of the polyethylene resulting in imbalance and poor implant performance. Lower stress under equivalent force (or higher contact area) has been demonstrated to contribute to higher wear rates. The goal of this test is to identify the sweet spot between the two scenarios.
Hani Haider et al. have extensively researched wear of knee implants, and discuss their findings in the article, “For Lower Wear of Total Knee Replacements, is Higher or Lower Contact Area Better?” [1]
Contact stress & contact area test methods
ASTM F2083 is the standard specification for testing a knee replacement prosthesis, including sections on classification, materials, performance, dimensions, finishing and marking, and packaging. Contact area and stress distribution testing requirements are outlined in section 6 of the standard and recommend replicating one of the published methods. Testing should be performed at various flexion angles: 0°, 15°, 30°, 60°, 90°, and the maximum angle if the implant is designed for deep flexion. Additionally, internal and external rotations of 15° are recommended for 90° and the deep flexion angle.
For contact area and contact pressure testing, several types of physical sensors can be used and are placed between the femur and the tibial insert.
Fujifilm pressure testing
Fujifilm is a paper-based system that utilizes a red color density variation to identify pressure gradients. The film is tested, scanned and evaluated via specialized software to identify both the contact area and the contact stresses. This analysis can result in higher contact areas than the Tekscan. The film may provide a more accurate contact area measurement since it is an “analog” film which doesn’t have gaps in between sensors.
A disadvantage for Fujifilm is that multiple films may need to be used to capture the contact stress range – potentially impacting the shape of the measurement and lower stress readings. Additionally, the paper film often creates artifact due to crinkling around rounded surfaces or edges resulting in a need to threshold or edit out some of the data set and is single-use with an expiration date.
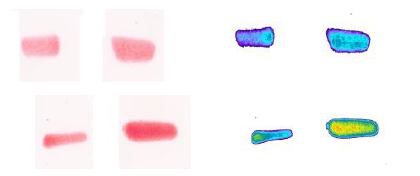
Tekscan pressure mapping
Tekscan is an electronic set of sensors that are laid out in various grid sizes on a thin matrix. It can be calibrated and provides real-time measurements as well as the ability to be re-used. The equipment outputs real-time readings of the force, pressure, and area measurements. It allows for adjustable sensitivities and doesn’t require stacking of films, eliminating noise or artifact. However, the software does have to interpolate between individual grid sensors which can result in lower contact areas than actual contact.
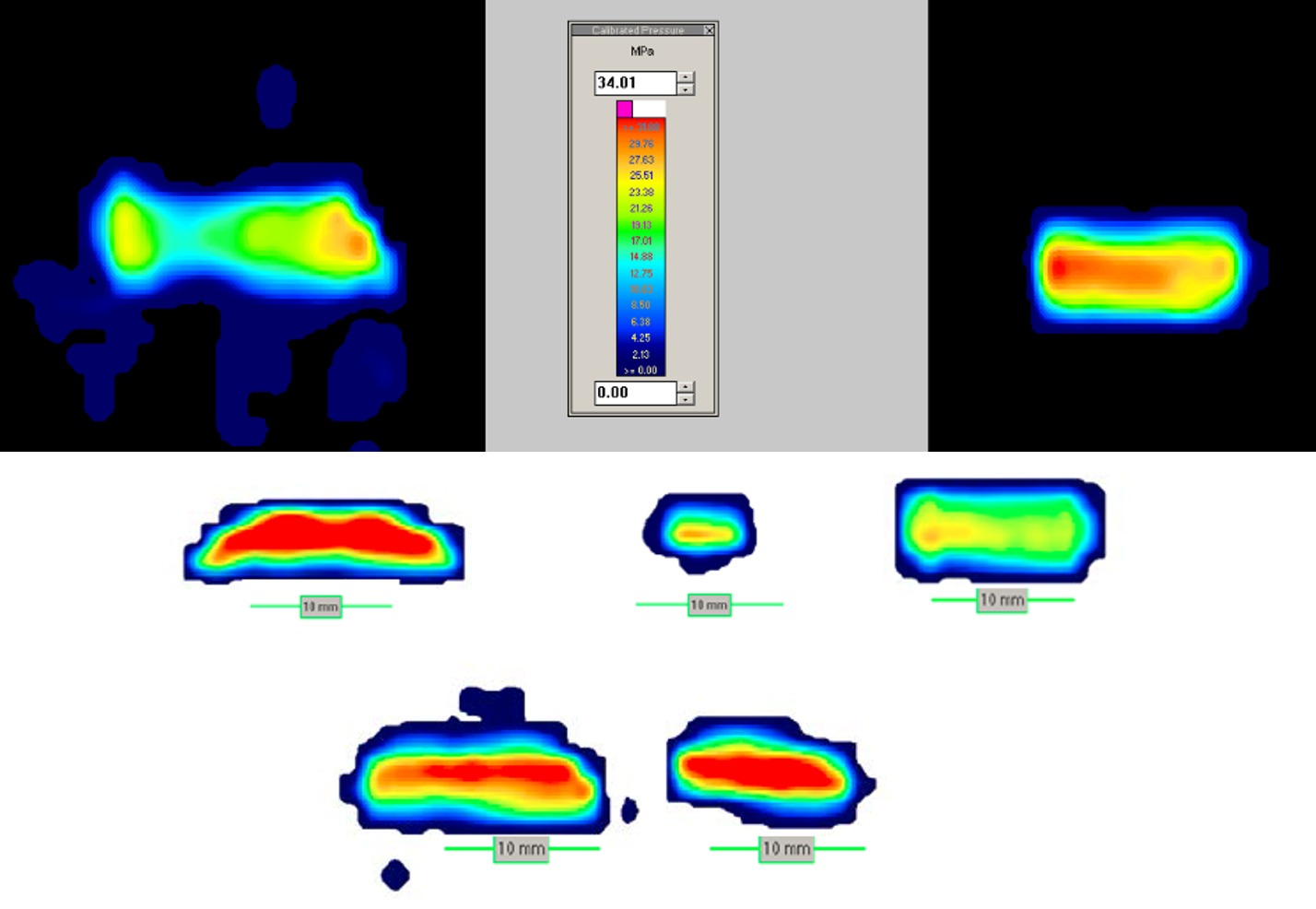
The sensors are placed between the angled femur and the polyethylene insert, and a range of forces simulating multiples of body weight (710 N) are applied. These can vary depending on the risk analysis, predicate data available, or objective of the test to evaluate different gait cycles. Testing should always be performed on virgin inserts if possible. If the inserts have been previously used, they should be inspected to ensure no permanent set has occurred otherwise the pressure gradients will not be accurate.
Another application for the contact stress and area testing is to evaluate the patella. ASTM F1672 outlines the requirements for a patella, as well as similar methods for testing. The flexion angles of 15°, 25°, and 90° are defined and respective loads of 377, 961, and 2,195 N should be applied. Additional angles can be evaluated as necessary. During testing, care should be taken to align the appropriate flexion angles with the translation of the patella in the trochlear groove to its expected position.
Contact area and contact stress testing are also useful for identifying the worst-case configuration for other types of knee testing – like ISO 14243 Knee wear.
Contact stress data acquisition
After completing the test, the data is best shown by angle and a contact area versus stress range graph. UHMWPE has a yield stress of around 40 MPa and understanding how the stresses will impact the mechanical integrity of the insert is critical to the long term success of the patient.
While there are advantages and disadvantages to both types of sensors, Element utilizes the Tekscan system to provide the most accurate data – allowing for real-time adjustments to ensure the testing is optimized.
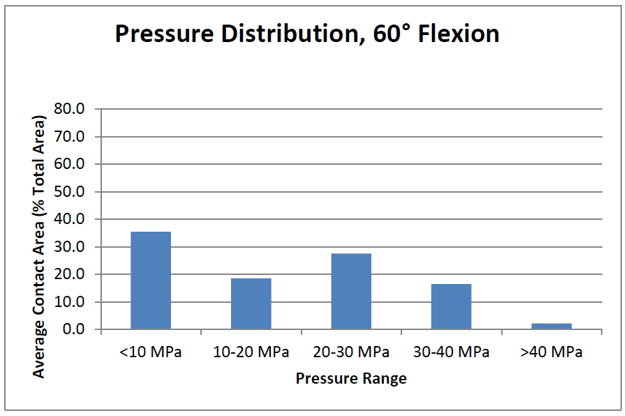
The Element advantage
As ASTM works to develop a test specification, our medical device experts routinely perform contact stress and area testing for total knee replacements, as well as wrist, ankle and other joint replacement implants. Contact stress analysis is useful where any two junctions come together, creating an understanding of stress risers, even load distribution, and confirmation of expected contact.
Element has one of the most expansive medical device testing scopes in the world, ranging from orthopedics and cardiovascular implants testing to EMC/EMI/product safety testing, and biological and packaging evaluations. We strive to meet all your medical device testing needs in the most expedient, efficient and responsive way. Contact us today.
Reference
[1] Hani Haider1, Joel N Weisenburger, Beau S Konigsberg2, Curtis W Hartman, Kevin L Garvin3 – University of Nebraska Medical Center
Find related Resources
Related Services
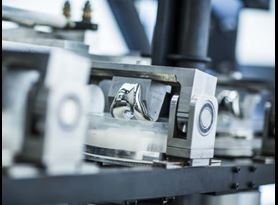
Fatigue Testing of Femoral Knee Components
Fatigue testing of femoral knee components is an important step in the validation process to ensure patient safety and device longevity. Learn from our Engaged Experts.
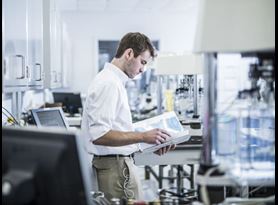
Test Protocol for Medical Devices
A protocol and plan will mitigate your risk, prevent confusion, set clear expectations, and preserve the necessary information for future reference and use.
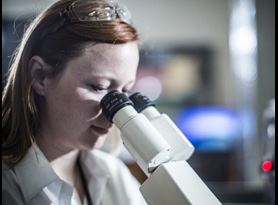
Preventing Fretting Corrosion of Orthopedic Devices
The human body is a corrosive environment that can compromise the performance of orthopedic devices. The test methods outlined in this article aid in preventing fretting corrosion in your device designs.
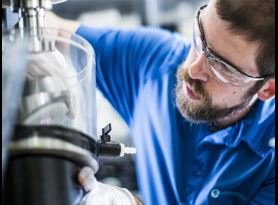
Orthopedic Implant Testing
As a global leader in orthopedic implant testing, Element has years of experience in evaluating hip replacements, knee prostheses, spinal devices and many other implants.