Maximizing returns from your door and window test program

Mark West is a recognized expert in the fenestration industry with 15 years of experience in product testing and certification.
Manufacturers often fail to get the most benefit from their testing programs. This article suggests how manufacturers can prepare their samples for door and window testing, learn from any failures and ultimately maximize their return on investment.
Sample preparation
When selecting a window or door set for testing, you should aim to provide the largest test sample possible, as most certification bodies will be able to assess reductions in size but not an increase. Maximize the size of your test sample, ensuring it stays within the capability of the test laboratory. However, don’t be tempted to manufacture something you will never realistically sell, as you may incur failures due to the size of the sample or risk over-engineering a product to perform at unrealistic sizes.
Your test samples should be well-fitted in a quality softwood subframe. Ensure the material is planed and, most importantly, straight and true and not bowed or twisted. A bowed or poorly- fitted subframe can pull your door or window samples out of square.
All glazing for PAS24 security testing must be replaced with toughened glass, which is mandated in the test standard to protect the testing engineer and increase the probability of a successful test. If the glass breaks during the test, the result is declared void and, the product cannot be classified as a pass or a fail.
A weather test is the same regardless of the configuration of the doorset or window. Security testing of a window or doorset will be more cost-effective if you are testing multiple casements within the same frame.
A window with a side-hung next to a top-hung over a fixed casement is effectively three tests for the price of one. By maximizing the casement sizes, you can gain approval for the longest possible transom and mullion. This type of window will also usually infer side-hung and top-hung windows performance without fixed panes and side-hung next to fixed and top-hung over fixed.
Where possible, you should include glazing, door closers and door furniture such as viewers and letterplates in your doorset test sample. Including these elements will make little difference to the performance in testing (providing the components have approval to applicable standards), but you will benefit from the added reassurance given to your customers when they see these items listed in the report in black and white.
When testing doorsets to PAS24 with multiple leaves, consider including a different glazing pattern in each leaf. Introducing midrails, solid panels in profile door leaves and different glazing styles in solid leaves will potentially increase your scope within the same test.
How many samples to provide
The laboratory will guide you on the number of test samples required for the testing involved. The number of samples needed is typically the minimum number specified in the standard. You can increase this number and further decrease the risk of cumulative damage or have additional samples available in case of failure. However, the suggested minimum number is usually optimum for customers when sample production and transport costs are considered. Weather testing and operational testing are usually non-destructive, allowing you to re-purpose the product for other testing.
In theory, if testing commences with weathertightness, followed by operation and strength and cycling and finishing with security testing, it should be possible to reduce the number of samples required for a full doorset PAS24 program from five to three. However, you should be aware that optimizing test samples in this way and saving the most destructive tests until last can be counter-productive.
Suppose a subsequent failure occurs in security testing. In that case, you will be several weeks into a test program and have a full suite of weather and operational testing results on a product that may never pass the security test. For that reason, it always makes sense to undertake the arduous security testing first.
Attend the test and learn
Attending the testing program in person or remotely allows you to understand how your product has performed against the rigorous test standards. Witnessing also allows you to understand failures, improvement possibilities and have immediate feedback from our technical experts.
Take full advantage of the testing process by ensuring that someone from your team is present. The testing will be a learning exercise. It can often be advantageous to bring along colleagues involved in the manufacture of the products to help them understand the pressures that samples are put under and how vital the smallest overlooked detail may be.
You should treat any failure as a learning exercise and ask the testing engineers why the product failed. Witnessing a failure, understanding why it happened and learning how to prevent a reoccurrence will significantly improve the chances of passing a re-test. Also, witnessing a ‘close pass’ will highlight potential product weaknesses and help you improve the product, preventing future failures that may have been ignored based on a successful test. We recommend that samples are collected for further examination and education of staff. This is particularly valuable in the case of samples that have failed.
Preparing for weathertightness testing
Ensure that the product is sufficiently sealed with mastic, paying particular attention to the joint between the frame and subframe joint. An inferior joint can cause additional air leakage or, at worst, a void test. Check whether any drainage holes have been included if required and a clear path for water to drain away. Do not be tempted to overdo the silicone for sealing, as you will be required to include any adjustments from the test samples to the production process. Any deviation from the tested specification will invalidate your test report. For this reason, never do anything to the sample that you would not be willing to repeat on every product in the factory. This applies to all testing.
Preparing for operational and strength testing
This operation and strength test is set up to evaluate the doorset or window itself; hardware items such as locks and hinges should/will have already been tested in their own right for durability. Failures usually occur due to poor preparation of the sample or insufficient care in the setup, including poor positioning of keeps. This can result in binding of the door or window on the threshold/frame or rubbing/grinding of the hardware against keeps resulting in increased operating forces outside of the normal range and, eventually, hardware failure.
When hardware is tested in isolation, it is usually in a frictionless environment in a calibrated test rig. You should check the operation of your doorset or window in the test rig before commencing cycle testing at the laboratory. Test engineers will install the sample in the test rig and fit the product to make it run, but they are not experts in a particular product and a doorset slightly out of square could result in failure. Doorsets and windows rarely fail these tests due to hardware specifications, and a well-specified product can fail the test if it is poorly installed.
Preparing for security testing
The security test is often a test of the actual specification and attention to detail in the manufacturing process. Precise setup and operation of the doorset or window to operate smoothly are less essential. You should ensure that attention has been paid to machining details around locks and keeps and screw fixings for locks and hinges. Removing too much material around a lock casing or a lock bolt mortice will make the product weaker. A threaded screw hole can pull out more easily, or a wood screw inserted without pilot drilling first can cause splitting of timber, both resulting in a premature test failure. Always ensure that locking bolts have sufficient engagement in their keeps.
Ensure any hinge, locking, or security points designed to be positioned less than 100mm of each other are fitted accurately. If the distance between two points is greater than 100mm, these will be treated as separate points in mechanical load and impact testing and increase the number of loads/impacts the door or window will have to take.
The Element advantage
Element provides a range of testing capabilities for doors and windows to ensure products are cost-effective and technologically advanced, as well as remain safe and fit-for-purpose throughout their lifecycle. Whether testing to a standard method or developing a custom program, our engaged experts can provide you with accurate, reliable results for projects small or large.
Contact our colleagues for more information.
Find related Resources
Get white papers, updates and event invites
Subscribe to content updates
More from Element
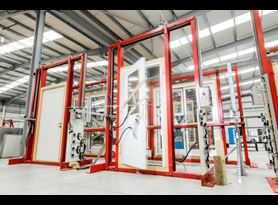
Door and Window Testing
See our range of door and window testing services
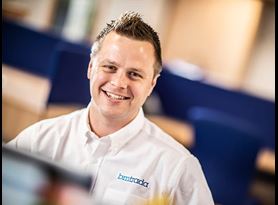
Certification Services
BM TRADA’s certification team of engaged experts provide a wide range of certification to services to a diverse range of industry sectors. Learn more about BM TRADA certification by visiting their website.
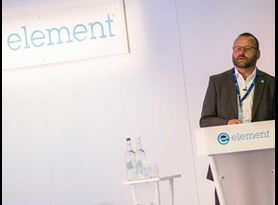
Resources
Discover blog posts, articles, white papers, webinars, and advice from our world-leading testing, inspection, and certification experts.
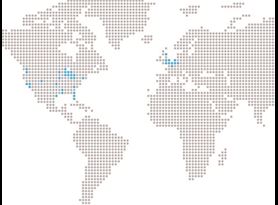
Element Locations
Learn more about our laboratories - where they are located; the unique capabilities they have and how they can help you solve your technical and commercial challenges.