Development of a Fast-Solving, Physics-Based Comminution Model for a Global Mining Company

Jon Douglas is an engineering consultant with over twenty-five years of experience across a wide range of sectors including nuclear, gas turbines, renewables, aerospace, and general industry.
Crushed rock forms the foundation of our society. With growing demand for sustainability, the need for improving the performance and efficiency of rock crushing equipment is becoming increasingly important for mining companies.
Background: DEM mining solution
Element’s Digital Engineering team has recently worked with a global mining company to optimize the design of their rock crushing (or “comminution”) machines, to improve performance, enable energy efficiency, and extend lifetime estimates.
To achieve this, our experts developed a physics-based, Discrete Element Model (DEM) of the mining equipment to enable a simulation of the crushing process. The DEM model allowed the team to simulate the rock breakage process of any given design, which allowed the customer to select the most efficient one for their needs.
The challenge
Unfortunately, the solution of this model required significant computational time and the team needed to assess a large number of design cases to optimize the setup. It was, therefore, essential to speed up the solution time. This was achieved by developing a Reduced Order semi-analytical Model (ROM) that combines physics-based breakage models with machine learning surrogate models, using impact data obtained from a reduced set of non-breakage DEM simulations.
The ROM uses a data science solution that utilized results from the DEM model simulations. We minimized the DEM model solutions required to provide sufficient data to the machine learning algorithm. This allowed the algorithm to develop relationships between the sizes of rocks that result from the changes to the input variables. The algorithm also assessed the impact that changes to input variables have on metrics such as machine wear. We used a Bayesian Design of Experiments technique to decide on the DEM simulations needed to train the ROM.
The solution
Once our client started using this technology, they inevitably asked the question, “Can we use it to optimize the design of a crusher?”. Our experts developed a solution to provide our client with answers to questions like “What inputs do I need to achieve a target output?” and “What inputs do I need to achieve a range of outputs when I’m uncertain about the exact value of some of the output quantities?”
The result
The resulting predictive tools allowed our client to confidently optimize their comminution machinery. The engineers can now quickly make changes to the operation of the in-service machinery to maintain consistent output. They can also easily develop new machines for future applications to sustain consistent production across their global operations.
Contact our experts to learn how our modeling, simulation, and optimization services can increase the efficiency of your operations.
Find related Resources
Related Services

Modeling and Simulation
We specialize in modeling and simulation to accelerate your research and development initiatives, optimize your designs and support safe, efficient operations.
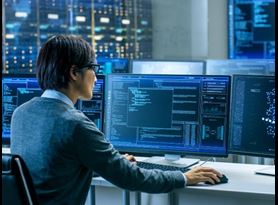
Digital Engineering Data Science and Machine Learning Services
Our Machine Learning and Data Science services offer customized solutions to transform your data into actionable insights.
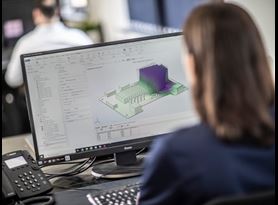
Finite Element Analysis Services (FEA)
Element offers advanced numerical analysis service using Finite Element Analysis (FEA) techniques using industry standard software to predict the long term behavior of materials components and products when in service.
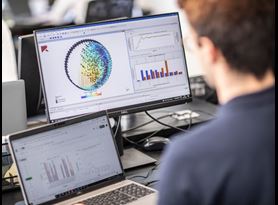
Discrete Element Method (DEM)
Our Discrete Element Method (DEM) services deliver innovative solutions that have helped companies across a wide range of industries.