Using Failure Analysis to Manage In-Service Occurrences
In-service occurrences have the potential to cause millions of pounds worth of damage to an organization in terms of not only lost business but also reputation. When an in-service occurrence takes place, it is therefore vital that the reason behind how and why a material or product has failed is established as quickly as possible, and a solution is found and put into place without delay.
Failure analysis is not only a critical aspect of product development and system improvement, it is essential to prevent future issues. Finding the root cause, or causes, for such an occurrence, however, is not an easy process and needs to consider not only all the relevant design information and service life to date but also the type of application as well as any environmental factors that have the potential to either cause or contribute to the occurrence.
The Rolls-Royce approach
Rolls-Royce has its own dedicated team of expert engineers supporting its core businesses with potential in-service occurrences. Working out of Rolls-Royce’s cutting-edge test facilities in Dahlewitz, Germany, the engineers carry out a wide range of unique materials testing, such as multiaxial fatigue capabilities, component vibration testing, and large-scale spin testing.
Through the Rolls-Royce/Element partnership, the Rolls Royce team are now bringing this expertise to multiple sectors, from energy and agriculture to automotive, aerospace, and transport, providing access to the same high-quality testing capabilities and service that Rolls-Royce uses every day to test its engines, materials, and components.
Understanding and replicating the occurrence
The first step in managing an in-service occurrence is to take as much information from the customer as possible regarding the problem, whether it is a blade crack, pipe rupture, sensor/connector failure, or something more unusual.
The Rolls-Royce engineers, each with different areas of specialist expertise, work together as a fully integrated product team and, if immediate data is lacking on the event, will carry out pre-analysis and pre-measurement to collate the necessary information. This might include analyzing and measuring the vibration behavior or executing a modal analysis and replicating failure mode.
If required, the team has the capability to measure the in-service situation of an accessory or component in mounted condition via Experimental Modal Analysis (EMA).
During this early stage of the process, the key objective is to gain a full understanding of the system in question. This enables the team to move on to analyzing and replicating real boundary conditions in the test setup, carefully reproducing and observing the issue whilst precisely matching the behavior.
Work towards proof testing an improved design
The next stage in the process is to verify the failure mechanism and make recommendations of how to identify resolutions. At this point, the team will start working towards proof testing an improved design to provide a tailored solution that will prevent future in-service failures.
Whilst the scope of a project will evolve as the testing is carried out, the team always starts at zero and tailors and adapts the testing as it progresses with the aim of producing a solution as quickly as possible.
A highly flexible and multi-faceted approach
Determining how and why a product or material has failed requires the expert application of a wide variety of analytical methods and tools. Rolls-Royce’s extensive test facilities allow for a highly flexible, multi-faceted approach in which every potential cause and solution can be fully explored. This involves being able to select from a wide range of testing methods to identify the procedure that will most accurately replicate the environmental conditions and in-field vibrations for the component. This could include shock testing, high-level reverberant acoustic noise testing, linear/angular acceleration testing as well as one or more vibration test procedures.
Combining multiple test types into a single testing program
The process will often include combining multiple test types into a single testing program to analyze how two or more factors being applied simultaneously may affect the test outcome. For instance, applying vibration testing and static loading simultaneously.
The team’s expert knowledge of the different methods allows for many of the procedures to be planned and executed in extremely short timeframes. The team’s piezo testing experts, for example, are able to calculate any frequency and put the system together in 30 minutes to test components, such as turbine blades, at an ultra-high frequency.
The team is also experienced at studying the vibration behavior of highly complex structures with 3D Digital Image Correlation (DIC), a 3D full-field, non-contact optical technique to measure contour, deformation, vibration, and strain on almost any material. This can be extremely useful for intricate pipe systems, reducing the need for multiple strain gauges.
Depending on the in-service occurrence, the test program may incorporate additional failure analysis procedures such as: examining the effect of corrosion including residue identification and corrosion prevention; fractography analysis in which the fracture surface is examined to determine the cause of the failure; chemical analysis to understand if the chemical composition of a material or the chemical processes used during manufacture may have contributed to the failure; and residue analysis which can help identify residual deposits on a material and determine whether this is a surface stain or a product of corrosion or material failure.
For more information about managing in-service occurrences and building a robust failure analysis testing program, please contact us here.
Related Services
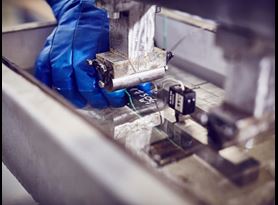
Failure Analysis in the Oil and Gas Industry
Watch our on-demand webinar with Element’s globally based, international experts will help you to understand and avoid failures in the Oil and Gas industry.
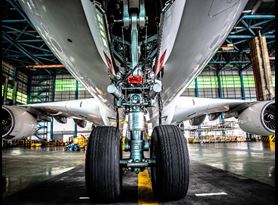
Fundamentals of Aerospace Failure Analysis
Learn about the the scientific method-based approach to establishing cause and effect can be used across all phases of a product’s lifecycle, from prototyping and testing to in-service maintenance and repairs.
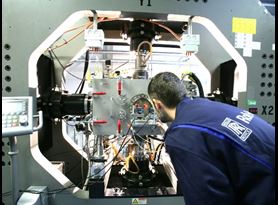
Element and Rolls-Royce collaborate to expand test services to their customers
The new agreement will provide Element’s customers with access to the cutting-edge rig and component test capability and engineering expertise of Rolls-Royce in Germany.
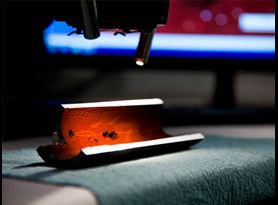
Failure Analysis
Find out how Element's global team of failure analysis experts learn from the past, to help prevent failures in service.