Magnetic Particle Testing of Flanges
Magnetic Particle Testing (MPT)
What’s the attraction?
Magnetic particle inspection is a method of detecting flaws in ferrous materials using magnetic fields. Surface and near-surface indications can be observed. This testing is best suited to magnetic materials, such as iron, nickel, cobalt, and their alloys. By inducing a magnetic field into the part and applying specially coated iron particles, surface or near-surface indications can be seen.
MPT can be applied to various forms of materials and components including billets, bars, tubing, extrusions, castings, forgings, fasteners, and weldments. All are commonly tested using magnetic particle inspection.
Depending on the application, wet or dry method can be used. In both methods the material is magnetically charged and iron particles are applied to the part for inspection of discontinuities. If a crack or defect is present, an opening in the material creates a leakage in the magnetic field, causing the particles to attract. This is like iron particles being attracted to the ends of a horseshoe magnet.
Key usage of MPT in the oil and gas sector
Element has decades of experience in providing a comprehensive range of oil and gas testing services enabling critical materials to be tested, inspected, and certified. We understand the complex challenges of transporting fuel and fluids in a reliable, efficient, and safe way.
Magnetic particle testing supports upstream, midstream, and downstream markets to ensure the safety and integrity of production and storage infrastructure, pipes, and pipeline systems, refineries, and tanks.
By examining the nature, location and extent of an indication, our highly trained and experienced inspectors can determine the origin and cause of both surface and near-surface discontinuities. These evaluations are critical both before and after the materials are sold into production, ensuring the production cycle is consistent and safe.
The use of MPT for sample verification
Magnetic particle testing of two discharge connection samples
Magnetic particle inspection was used to determine the evidence of any surface or subsurface discontinuities on two discharge connection flange samples. The testing was performed on a Magnaflux H-700 unit using the wet fluorescent method.
The level II certified engineer visually inspected the sample for any surface indications prior to testing and verified the current equipment calibration on both the machine and ultraviolet lamp to be used during the inspection. Black light intensity and white light were measured to verify ideal inspection conditions using a Gould-Bass DLM-1000 light meter.
The samples were placed between the headstocks of the machine and the continuous flow method was applied. The electrical current was introduced though the sample and fluorescent bath particles were introduced with the current engaged. A calibrated black light was used to inspect the sample for any signs of defects or indications.
No indications were found on the two samples. They were cleaned and demagnetized using A/C withdrawal method in a Magnaflux Demag Unit.
The samples were reported as acceptable to the client, which satisfied the sample requirement for that lot of parts.
Read more about Non-Destructive Testing Services and Magnetic Particle Testing.
Find related Resources
More from Element
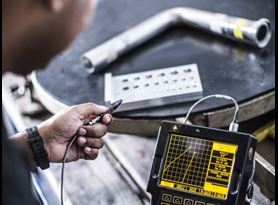
Eddy Current
Eddy current inspection is an efficient and precise non destructive test method. This type of inspection is particularly helpful to evaluate heat exchangers and aircraft parts and components.
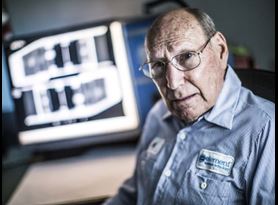
Radiographic Inspection Services
Element’s radiographic inspection laboratories provide testing for a wide array of sectors. Our global experts advise on the most suitable testing methods to ensure your materials and products are fit for purpose.
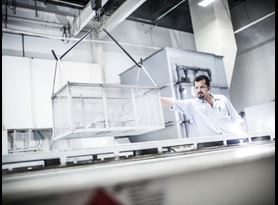
Liquid Penetrant Inspection (LPI)
Liquid penetrant inspection (LPI), or dye penetrant inspection, is a reliable and cost-effective method for detecting surface flaws of welds, castings, and other components that cannot be destroyed. Our experts can conduct comprehensive on-site penetrant inspection.
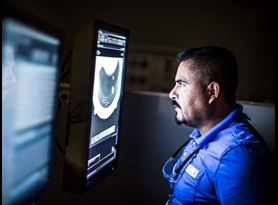
Non-Destructive Testing (NDT)
Element's NDT services comply with a wide variety of industry standards, government contracts, military specifications and unique customer requirements.