Testing Fluids Systems for Hybrid and Electric Vehicles
Although most vehicle manufacturers now produce electric or hybrid options, these vehicle designs are still very new compared to conventional internal combustion engines, and the design and manufacturing processes still present unknowns. Designing vehicle fluid systems that are optimized for EVs is an engineering challenge. The most specialized fluid system in an EV is the battery cooling system, but there are other fluid systems whose designs also must be modified for use in an electric vehicle.
Although the designs of battery modules and packs are undergoing constant innovation to improve performance and durability, rearranging battery components can have significant and sometimes unpredictable effects on the battery’s thermal regulation. Laboratory testing is the most reliable way to predict a fluid cooling system’s performance under realistic environmental extremes while the vehicle is still in the design phase. As cooling systems for modern vehicle batteries are constantly evolving, manufacturers must rely on experienced engineers and technicians to establish relevant test parameters and generate meaningful and informative results.
Battery cooling systems testing
Currently, Element is partnering with a major manufacturer to test EV battery cooling plates and their associated tubes, lines, and connectors. The manufacturer will receive reliable data that will help them to refine and rewrite internal procedures as a result of this testing, which primarily includes thermal cycling and pressure pulsation. During these tests, coolant is circulated through the plates at varying temperatures and pressures while a range of environmental extremes, including external temperatures from -30°C to over 100°C are applied simultaneously. Element will also supply the manufacturer with data regarding the performance of the plates upon startup, as technicians evaluate flow characteristics of the coolant through the plates using typical flow rates at low temperatures.
Other Fluids Systems in hybrid and electric vehicles
In addition to their specialized battery cooling systems, hybrid and electric vehicles share some fluid systems with traditional internal combustion engines, including hydraulics systems for brakes, transmission and steering fluid systems, and cooling systems for radiators. The components of an EV differ from those of an internal combustion vehicle; EVs also tend to be significantly heavier and have a different weight distribution. This can affect the functionality of other fluid systems in the vehicle, such as hydraulic steering and brake systems, requiring that those systems be redesigned. For many vehicles, especially novel vehicles, full vehicle lab testing is required to understand how systems affect one another, and how this might impact handling, safety, and longevity.
How can Element help?
Element anticipates, rather than reacts, to industry changes. It is our investment in advanced testing technology and in experts with specialized expertise that make this approach possible. Testing standards for hybrid and electric vehicles are still developing, and many tests on new vehicles must be custom designed. Only the most experienced technicians and engineers can ensure tests are designed correctly and results are accurately interpreted. A partnership with Element can help avoid production delays and costly redesigns. Our knowledgeable engineers and technicians work alongside clients throughout the product lifecycle, from research and development to full vehicle testing, providing consultancy and testing support that meets evolving industry standards.
For more information about Element’s specialized facilities and our testing options for hybrids, EVs and vehicle fluids systems of all kinds, contact us.
Find related Resources
Learn more
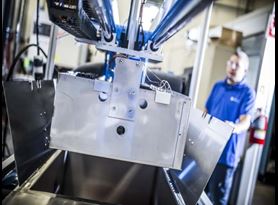
Hybrid & Electric Vehicle Battery Testing
We perform validation testing on Li-ion and Ni-MH battery cells, modules, ultracapacitors and packs to ensure the safety and performance of your products.
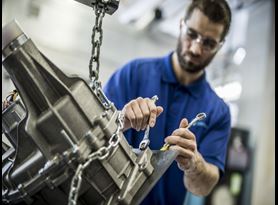
Full Vehicle Durability Testing
Learn about Element’s durability testing methods for vehicles including vibration testing, environmental simulation, weathering, and dynamics testing.
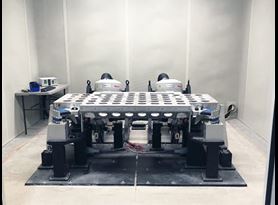
Automotive Buzz, Squeak & Rattle Testing
Element’s large multiaxial silent shaker can perform buzz, squeak, and rattle (BSR) testing with fast turnaround times on components up to 700lbs, to help manufacturers create quieter products.
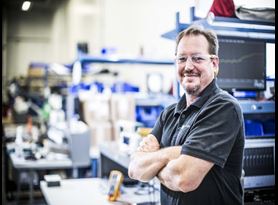
Automotive Hose Testing
Accurate and reliable automotive hose testing programs from Element help ensure that your critical hoses, lines, and flow systems will work under the most stringent standards.