Understanding the Fundamentals of Vibration Analysis

Jon Douglas is an engineering consultant with over twenty-five years of experience across a wide range of sectors including nuclear, gas turbines, renewables, aerospace, and general industry.
At Element, we use vibration analysis to characterize the vibration levels experienced, or generated, by equipment. The objective is to determine the level of vibration and its frequency content and understand how that relates to the dynamic characteristics of the equipment of interest.
Applications include:
- Characterizing the vibration environment to design and test a product that will be deployed within that environment
- Characterizing the vibration generated by equipment to ensure compatibility with other equipment that will be located in the same vicinity
- Monitoring vibration over an extended period to determine any changes that might occur due to wear and /or degradation
Element’s engaged experts support all of these applications with a variety of toolsets, including;
- A broad range of vibration test facilities that are used to carry out vibration testing and shock qualification testing
- Computational analysis methods including Finite Element Analysis
Preparing for vibration analysis
Vibration analysis can only ever be as good as the data that is analyzed. Consequently, before vibration measurements are carried out, it is essential to evaluate what is required from the measurements and to ensure the veracity of the vibration data to be analyzed. This means ensuring the most appropriate vibration measurement method and instrumentation have been employed to accurately record the vibration over the appropriate frequency range. This in itself is a specialist activity (which Element carries out for a broad range of different engineering applications).
Once the vibration has been measured and recorded (usually as acceleration time-domain data), the vibration analyst must have the expertise to recognize the potential benefits and limitations of the different types of analysis that are available. Typically, Element’s vibration analysts work closely with the client, such as with Rolls-Royce working to understand the dynamic characteristics of engine components or Ocado developing new equipment that is required to withstand earthquake environments.
How is vibration measured?
Vibration can be measured in different forms such as:
- Acceleration - the rate at which the velocity changes.
- Displacement - the distance that the measuring point has moved.
- Velocity - how fast the movement is.
The choice of which parameters to use is usually determined by the application.
Acceleration, which is the most commonly used parameter, is measured with a transducer called an accelerometer, which can detect vibration over a broad frequency range and generates an output signal directly proportional to the acceleration level of the item on which it is mounted.
Displacement transducers are most suitable for measuring low-frequency vibration, where low acceleration levels are present but the vibration displacement is significant.
Velocity transducers are the least common and may be used for applications, such as condition monitoring, where velocity levels are most commonly referenced, and they also only require simple differentiation or integration to convert the velocity signal to acceleration or displacement, respectively.
The vibration signals from the transducers are recorded by a datalogger that typically converts the analogue signals to digital before storing them. The setup and operation of such dataloggers is again an area that requires some knowledge to ensure that the signals are not modified during the recording process.
How is the vibration data analyzed?
Vibration testing data is typically analyzed in the time and/or frequency domain. Time domain vibration analysis monitors vibrations using a time waveform which is the recording of acceleration versus time. Displayed on an electronic test instrument called an oscilloscope or signal analyzer, a time waveform can then be reported in graph form to observe changes.
When recording the vibration signals, it is good practice to view the vibration signals in the time domain (as time histories) before and during the recording, as any signal corruption, noise, or intermittent faults in the instrument chain can be observed. Time domain analysis can be used to evaluate the peak accelerations that are present, indicating the overall condition of a component or piece of equipment and subsequently used in conjunction with defined acceptable operational vibration limits to forewarn of any faults that are developing, due to wear and tear or fatigue.
Frequency domain vibration analysis
Frequency domain vibration analysis, or spectrum analysis, is used to observe the frequency content of the vibration and can show changes that may not be picked up by just observing the time waveform. As all signals are acquired in the time domain, a time history (time waveform) must be transformed into a spectrum to enable analysis in the frequency domain. The most common method of transformation uses the Fast Fourier Transform (FFT), an algorithm that converts a signal from the time domain to the frequency domain. Digital signal analyzers (often called FFT Analyzers) are used to perform frequency analysis on a waveform and these analyzers are used extensively to characterize vibration; to determine any changes in vibration over time or to investigate unexpected vibration sources or in-service failures suspected of being caused by the vibration environment.
Understanding the peak acceleration levels and frequency content of vibration waveforms can be critical for protecting sensitive equipment, for designing equipment to withstand a variety of vibrations, such as that experienced by rotating components, and to identify issues such as misalignment.
Digital signal analyzer vibration analysis
Digital signal analyzers typically offer a wide range of tools with which to review both the time-history signals and the frequency spectra.
These tools include:
- Automatic identification of acceleration peaks and phase relationship (for time measurements),
- Identification of resonance frequencies and calculation of damping associated with resonance peaks, order analysis (characterization of harmonic peaks usually associated with rotating equipment)
- Power spectral density (PSD) analysis is commonly used to characterize and specify random vibration environments.
Additionally, digital signal analyzers can be used to perform mathematical operations on multiple separate signals, determining transfer functions and filtering over prescribed frequency ranges.
As with all vibration analysis, the operator must understand the implications of using a variety of analysis tools and setup parameters on the final analyzed signals.
Modal testing – determining the dynamic characteristics of a mechanical structure
Modal testing is the derivation of a mechanical model to describe the dynamic behavior of a structure by acquiring vibration measurements on the structure and analyzing them in such a way that the vibration modes (shapes associated with resonances) can be determined and visualized.
- Validate mathematical (finite element) models
- Understand in-service conditions (operating deflection shapes)
- Investigate or trouble-shoot vibration issues
- Assess the dynamic characteristics of prototypes/new designs
Typically, the component or assembly under test is excited with a small shaker or impact hammer, and the excitation force is measured. The acceleration response to the excitation is measured with accelerometers at several locations on the item and frequency response functions (response acceleration/input force) are recorded using a digital signal analyzer.
The response functions and locations at which they were made (geometry) are then converted into a modal model using modal testing software and the resulting model can be used to determine the modal parameters (resonance frequencies, damping values, vectors, and modal masses) and to visualize the mode shapes of the test item.
Alternatively, operating deflection shapes can be determined, as the name suggests, by measuring the acceleration response at a set of locations on a structure under operational vibration conditions. The modal test software can then be used to analyze the relative accelerations at the measurement locations and determine the vibration mode shapes.
Scanning laser doppler vibrometer with an excitation source
An alternative method for conducting modal testing and one that Element has the capability to carry out, is by using a Scanning Laser Doppler Vibrometer (SLDV). An SLDV, in conjunction with an excitation source, such as a small shaker, uses a scanning laser beam to measure the velocity on the surface of a structure that is the response to the controlled input vibration.
The modal testing software determines the modal parameters from the resulting response functions. The SLDV method has the advantage of using a non-contacting method to measure the vibration response and can be automated to record response at as many or as few locations as required, at a far greater speed than the traditional modal test method.
Using computational analysis methods to support vibration analysis
Our Digital Engineering team apply computational analysis methods, including Finite Element Analysis (FEA) to model components, assemblies and full systems to develop enhanced understanding of their performance in a vibrational environment.
Computer-based modeling techniques like these can play a key role across the product lifecycle. From identifying and correcting potential issues during the design process to optimizing and solving in-service product failure issues. Our engaged modeling experts work closely with colleagues in the physical testing team to both develop solutions and optimize physical testing to support validation.
In addition, Element’s vibration experts can help manufacturers evaluate the potential benefits of implementing a vibration monitoring system that can measure and record vibration signals in relation to pre-determined parameters and can be highly effective at managing ongoing risk to prevent serious failures.
To find out more information on vibration analysis and selecting the most appropriate vibration testing methods, please contact our experts.
Find related Resources
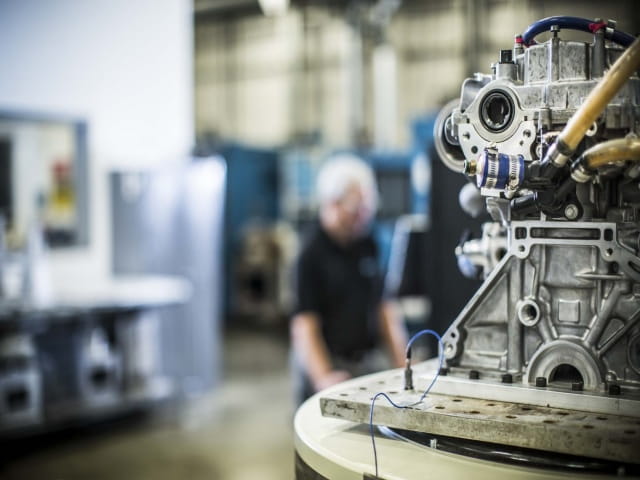
Choosing a Vibration Test Procedure
Choosing the right vibration testing protocol helps ensure that products can safely withstand the vibration levels they experience throughout their service life, ensuring product quality and safety. While most standards provide generic default test severities, more advanced procedures use existing data from product performance and operational environments to better replicate in-service conditions. Click here to read the full article.More from Element

Modeling and Simulation
We specialize in modeling and simulation to accelerate your research and development initiatives, optimize your designs and support safe, efficient operations.

Vibration Testing
Find out how Element's vibration testing services help to make certain that the products we test for our customers will perform safely and as expected when in the field.
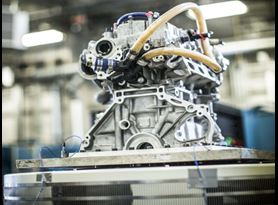
Vibration Testing of Complex Structures
Element and Rolls-Royce have joined forces in a unique collaboration to offer their vibration services to a wide range of industries from aviation and automotive to rail and oil and gas.
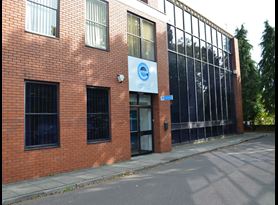
Element Warwick
Our Warwick site is our European Environmental Testing centre of excellence and an SC21 signatory site, with UKAS accreditation to BS EN ISO/IEC 17025:2005.